How Fluid Analysis with AI Improves Uptime and TCO
When you think about the causes of machine downtime, what immediately comes to mind? For a lot of people, it’s a part failure due to machine misuse or premature wear. […]
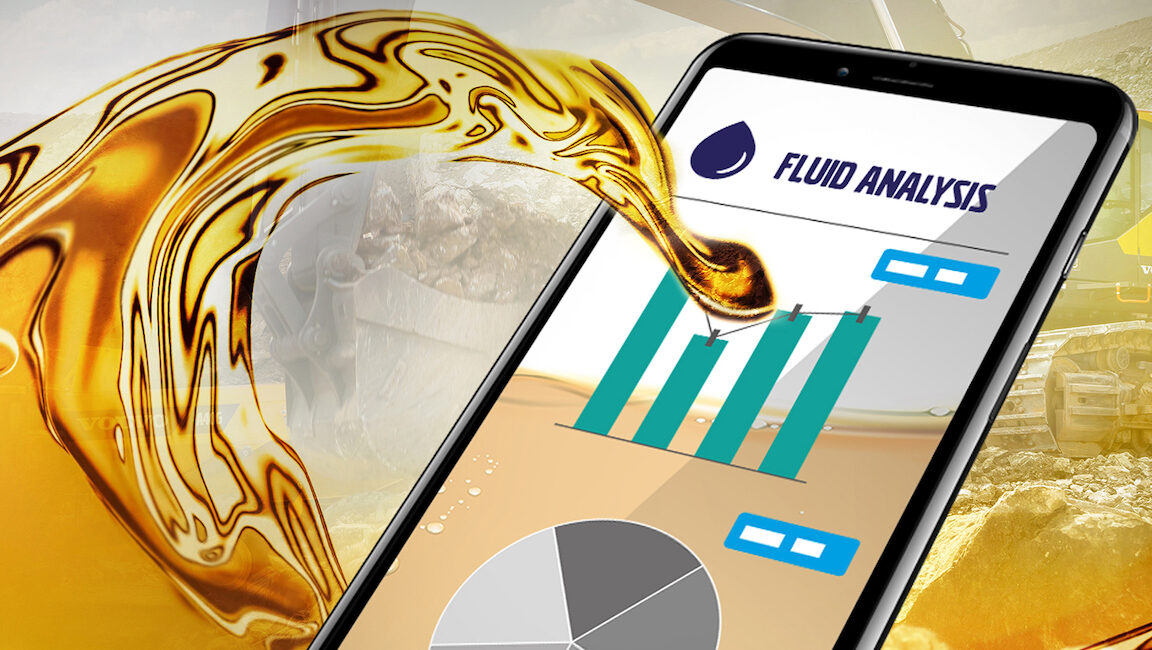
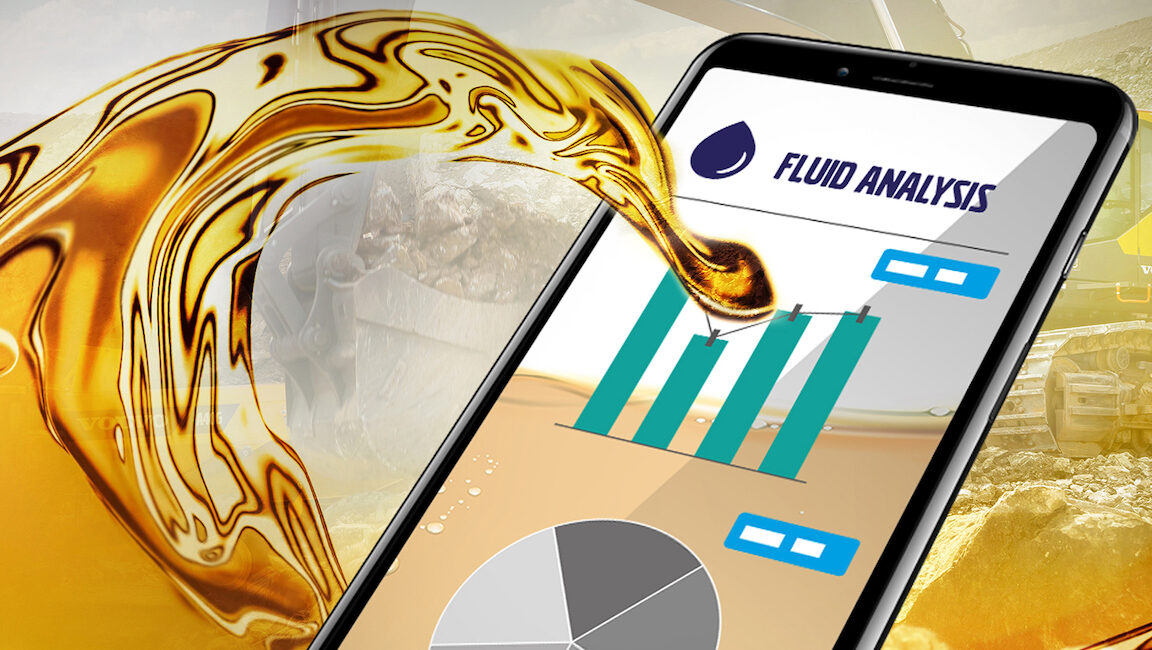
When you think about the causes of machine downtime, what immediately comes to mind? For a lot of people, it’s a part failure due to machine misuse or premature wear.
It may surprise you to hear that up to 75% of repair costs and downtime are related to contaminated lubricants and fuels, and about 66% of all bearing failures are because of lubrication issues. That makes it critical to properly manage fluids.
Here at Volvo, we’ve recently launched a Fluid Analysis service to help with this. Our Fluid Analysis program provides early warnings so customers can take preventive action as needed against contamination and wear, leading to improved uptime, extended machine life and a lower total cost of ownership.
The new Fluid Analysis program provides a thorough “health check” and encompasses lubricants, diesel fuels, diesel exhaust fluid (DEF) and coolants. It’s an expansion of our existing Oil Analysis program which provided machine’s vital systems with analysis of oils in the engine, transmission, hydraulic system, axles and brakes, with coolant and fuel upon request. With the new program, customers simply have more fluids examined for a more comprehensive checkup.
Fluid Analysis is our first artificial intelligence (AI) platform-driven analysis to identify wear metals and contaminants or changes in fluid conditions. The new process uses data analysis to provide easy-to-understand reports and insights to help customers make better decisions. AI accelerates the testing process, allowing lab technicians to focus on more pressing issues such as analyzing abnormal or critical samples.
The Fluid Analysis program also increases the number of testing labs to 20 global locations (four in North America) through a partnership with an industry-leading testing provider. This will allow all dealers and customers who take advantage of the program to benefit from worldwide data, reducing lead time and simplifying the sampling and analysis process.
How does fluid analysis work?
Customers can utilize the program through a service contract with their Volvo CE dealer and benefit from individual sample kits.
Once a fluid sample is taken from a machine, the dealer sends it to a lab where it’s analyzed and diagnosed based on any trace elements found. A highly visual and easy-to-analyze report with recommended actions is then shared via a cloud-based platform.
With routine fluid analysis and historical data, AI algorithms can identify trends, patterns and correlations that can reduce downtime by up to 15%. This program will make it much easier for our customers to reduce downtime, optimize costs and improve operational efficiency.
Learn more about our Uptime Services like this new program or contact your local Volvo CE dealer for additional details.
By Edward Goodchild, Head of Repair and Maintenance
Categories: Construction Equipment, Insights, Service